EL IMPACTO DE LOS DESPERDICIOS EN LA MANUFACTURA ¿SE PUEDE EVITAR EL DESPERDICIO EN LA INDUSTRIA?
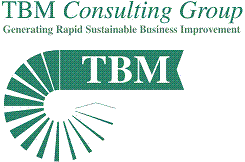
18 de agosto del 2011 | por Rodolfo Serralde Solórzano
∙ Para el 2030 se espera que el sector industrial represente aproximadamente el 30% del consumo final de energía, de acuerdo con la Comisión Nacional para el Uso Eficiente de la Energía.
∙ La Práctica de Energía Lean maximiza las inversiones en energía y elimina el desperdicio.
Cada vez más, las empresas están adoptando medidas adicionales para reducir y compensar los impactos ambientales de su consumo de energía. Estos pasos pueden mejorar las percepciones de los empleados y clientes respecto de los compromisos ambientales de la empresa, y ayudar a reducir su huella de gases de efecto invernadero.
Sin embargo, muchas empresas aún luchan porque sus altos ejecutivos presten atención al consumo de energía. La energía es a menudo vista como un costo necesario para hacer negocios, por lo que las iniciativas dirigidas a un uso eficiente de ésta pueden tener dificultades para competir por la atención de la organización ante otros requerimientos operativos.
De acuerdo con el Balance Nacional de Energía de 2009 de la Secretaría de Economía, en lo que se refiere a la distribución del consumo dentro del sector industrial de las ramas más intensivas en uso de energía, la siderurgia representó 11.8%, la industria cementera 9.6%, la azucarera 7.1%, a la industria Petroquímica de Pemex correspondió el 6.7%, la química 6.4%, la minera 5.1%, la industria de la celulosa y el papel aportó 4.0%, 3.9% vidrio, 1.4% de la cerveza y malta y el 3.8% restante las industrias de la construcción, aguas envasadas, automotriz, hulera, aluminio, fertilizantes y tabacalera.
Los manufactureros utilizan gas natural y energía a base de petróleo para manejar sus máquinas y plantas, como ingrediente en productos terminados y envases, y para transportar sus productos al mercado. En la mayoría de las empresas, 20% o más de los recursos naturales que consumen – electricidad, agua, gas, combustible y productos derivados, tales como vapor y aire comprimido – se desperdician.
Pero no todo se trata de moderar los costos, ya que las plantas de manufactura, en especial aquellas con operaciones 24 / 7 de proceso continuo, pueden ser usuarios intensos de energía; por lo que la reducción del consumo, incluso por unos pocos puntos porcentuales, puede tener un impacto ambiental enorme.
Herramientas Lean para el manejo de la energía
La manufactura esbelta o Lean es un modelo de negocios que enfatiza la eliminación del desperdicio al mismo tiempo que se entregan artículos de calidad con el menor costo para el fabricante y consumidores. En este contexto, “desperdicio” se refiere a las ineficiencias de cualquier tipo, abarcando desde tiempo, movimiento, energía y materiales.
«Se ha descubierto que el método Lean mejora el desempeño ambiental, aun cuando los esfuerzos no estén completamente dirigidos hacia el medio ambiente. Sin embargo, el impacto ambiental está integrado por la manufactura esbelta dentro de los llamados desperdicios. Además de que Lean crea una cultura organizacional muy enfocada a la minimización de desperdicios, prevención de contaminación, sistemas de administración ambiental y sustentabilidad”, comentó Michael Latuga, Director General de TBM Consulting Group México.
Aquí algunas herramientas de mejora continua y cómo pueden aplicarse a la eliminación de desperdicios energéticos, y de este modo reducir costos sustancialmente.
1. Las 5S: Limpieza y Organización en el Lugar de Trabajo
Las 5S a menudo es lugar en donde la mejora continua inicia en un área en particular. Los cinco términos, que empiezan con la letra S, describen una acción a utilizarse para crear y mantener la seguridad, organización y limpieza en un lugar de trabajo de alto rendimiento. Estas actividades son fundamentales para toda mejora y pueden aplicarse en cualquier lugar (células de trabajo, almacenes, oficinas, camiones de entrega, puertas de embarque, etc.).
Desde una perspectiva de administración, las 5S son una herramienta valiosa porque promueven la seguridad, crean un ambiente receptivo para el trabajo estándar, fomentan el control visual, ayudan a identificar el desperdicio y promueven la satisfacción de los empleados.
2. Trabajo Estándar: Repetición para Crear Procesos de Calidad
Reducir las variaciones mejora la calidad a través del reforzamiento de las especificaciones de un producto y/o invertir en la automatización, esta es la primera opción de los fabricantes. Pero las personas no pueden ser automatizadas, y la variación en las tareas que desempeñan puede originar desperdicio en movimientos, tiempo, materiales, maquinaria y energía. Estandarizar las tareas con instrucciones de trabajo estándar previene esto. Los procesos de alta calidad hacen uso de activos de la manera más eficiente posible, de este modo, consumen lo mínimo de activos (costos) para crear el valor máximo (utilidades).
La ventaja competitiva de ser un fabricante Lean viene no sólo de diseñar y crear productos, sino de diseñar y crear procesos Lean. Estandarizar las actividades diarias que comprenden los procesos, es clave para eliminar y mantener la calidad y, por lo tanto, la eficiencia energética.
3. Mantenimiento Productivo Total (TPM) y Mantenimiento Autónomo
Un punto focal en la reducción de energía en una planta de fabricación, es la maquinaria. Particularmente en industrias de procesos continuos, el piso de producción consume más energía que cualquier otra parte de la instalación. La herramienta de mejora continua ideal para atacar el desperdicio de energía en el piso de planta es el Mantenimiento Productivo Total o TPM (por sus siglas en inglés).
El objetivo del TPM es mantener el equipo en óptimas condiciones y apoyar los principios Lean. Fiel a la filosofía Lean, TPM resuelve los problemas; en este caso, se ocupa de las dificultades comunes de los equipos de producción, tales como la supervisión de las condiciones básicas del equipo, falta de conocimiento requerido para operar y dar mantenimiento o un mal diseño del equipo. El deterioro de los equipos no se atiende hasta que ocurre un mayor y más costoso problema, como una línea de ensamble detenida o la aparición de productos de baja calidad.
El mantenimiento del equipo debe formar parte del trabajo estándar de los operadores de la maquinaria para lograr una eficiencia óptima. A través de ese “mantenimiento autónomo”, los operadores no sólo realizarán tareas de mantenimiento estándar, sino que también se convertirán en un sistema de alerta temprana de anormalidades en el equipo. Cuanto antes sea detectada una anormalidad, más rápida podrá ser arreglada y menor será el impacto negativo en la producción.
4. Administración Visual
La administración visual se refiere al concepto de comunicar conocimientos pertinentes en un ambiente de procesos y condiciones a todos los que trabajan en este ambiente, a través de señales visuales. Además, permite a los empleados diferenciar entre una situación normal y una anormal de manera inmediata.
La administración visual “desmitifica” muchos de los lenguajes y métricas secretas utilizadas en los sistemas de administración por jerarquías, que deja la toma de decisiones a los altos ejecutivos. Por el contrario, los ambientes Lean requieren transparencia a fin de difundir el control de los procesos a aquellos quienes realizan el trabajo dentro de esos procesos, ya que:
∙ Promueve el aprendizaje continuo a través de la observación y atención;
∙ Determina el control y responsabilidad en manos de los empleados;
∙ Mejora el rendimiento al resaltar los problemas;
∙ Mejora la eficiencia al facilitar ver los desperdicios;
∙ Conecta las actividades diarias a las metas estratégicas, enfocándose y promoviendo el rendimiento que soportan los objetivos, y
∙ Desarrolla el compromiso, obligación y responsabilidad que crean el potencial de participación de todos los niveles de una organización en relación a la mejora del rendimiento.
Algunos ejemplos de herramientas operativas de administración visual pueden ser:
∙ Pizarrones donde se muestre el tiempo real y la tendencia de rendimiento, como resultados reales contra lo previsto, tiempos, consumo de energía y calidad obtenida.
∙ Sistemas con códigos de color para identificar a los responsables de áreas, herramientas, maquinarias, empleados, materiales, procesos, etc. Esto va en conjunto con las 5S posibilitando identificar el compromiso y obligación de manera inmediata.
∙ Centros de información con tablas, métricas, listas y otras muestras para comunicar el rendimiento por unidad, función, sistema, proceso, etc. Estos centros también sirven como puntos de reunión para estos grupos.
Estas herramientas promueven la eficiencia operativa, que a la larga, apoya el uso eficiente de energía.
Práctica de Energía Lean: Propuesta de TBM Consulting Group
La propuesta de TBM Consulting Group es la de adoptar una metodología de mejora continua que maximice las inversiones en energía y que elimine el desperdicio. La Energía LeanSigma es una metodología comprobada que puede hacer esto con la ventaja de utilizar herramientas familiares que los fabricantes ya utilizan para mejorar los procesos y que ofrece:
∙ Maneras de identificar, clasificar y priorizar el impacto financiero de la conservación de la energía.
∙ Mejorar el rendimiento de las emisiones ambientales, satisfacción de clientes y costos de operación.
∙ Una ventaja competitiva que permita crecer las ventas y utilidades.
∙ Una cultura de participación y respeto mutuo que favorezca la mejora continua.
Con base en lo anterior, los gerentes de planta pueden entender el consumo de energía en sus plantas, así como los costos relacionados a éste; aplicar los principios Lean para identificar oportunidades para ahorrar energía, cambiar los hábitos al incrementar la conciencia de los empleados, además de mantener las ganancias con el tiempo al integrar el trabajo estándar con prácticas ahorradoras de energía y métodos visuales para seguir el progreso. Adicionalmente, al capacitar a los asociados en identificar y eliminar el desperdicio de energía, una organización crea su propia liga de responsables del medio ambiente y puede rápidamente demostrar el poder de la mejora continua, ya que los ahorros son inmediatos.
“Al trabajar con nuestros clientes, en particular en la práctica de Energía de TBM, hemos encontrado que los Kaizens de Energía ayudan a comprometer a los empleados con más fuerza que cualquier otra iniciativa de mejora. No sólo están trabajando para reducir las facturas de los proveedores de servicios públicos, sino que están haciendo su parte para reducir la dependencia del país del petróleo extranjero, reducir las emisiones de gases de invernadero, y salvar el planeta”, comentó Michael Latuga.
Al vincular la administración de la energía con las actividades Lean, los esfuerzos de reducción de energía pueden unirse más con las iniciativas de mejora, consideradas por los altos ejecutivos como de vital importancia para el éxito del negocio. En efecto, las mejoras de energía pueden ir de la mano con las actividades Lean ofreciendo beneficios importantes en la empresa.
Para empezar: Muerte a las Fugas
Los proyectos Kaizen de Energía, que forman parte de la Práctica de Energía Lean de TBM Consulting Group, comienzan por identificar las fuentes de energía en la planta. Además del consumo excesivo de electricidad y otras fuentes de energía, tanto el gas natural como el aire comprimido, el vapor y las fugas de agua; cuestan a una fábrica cientos de miles de dólares por año.
Gas y aire comprimido – Reparar fugas produce ahorros inmediatos y sustanciales. Un cliente de TBM reparó 400 fugas de aire, dando como resultado importantes ahorros económicos. Después de reparar éstas, se dieron cuenta de que podían detener el consumo de dos compresores (450 HP y 200 HP) que usaban durante tres turnos.
Vapor – Las fugas de vapor no detectadas son extremadamente caras, como lo son las pipas y válvulas sin aislar en sistemas de vapor. Reparar fugas de vapor reduce drásticamente el desperdicio de energía.
Agua – Es común el derrame de sistemas que utilizan o abastecen agua hervida, tales como son los calentadores. Igual que con el aire comprimido, el agua a menudo es mal utilizada o desperdiciada tanto en los procesos de fabricación como en las rutinas de saneamiento asociadas con ellas.
Equipo eléctrico – El monitoreo y documentación del consumo de energía de equipo eléctrico demuestra qué tan eficiente opera el equipo. Es importante entender para qué se utiliza el equipo y si el mismo oculta algún proceso ineficiente.
Combustible de vehículos – La manera más efectiva de reducir los costos de combustible para vehículos es reducir la necesidad de transportación y manipulación de material. Estrategias de carga y descarga sin almacenaje (cross-docking) y embarques consolidados pueden reducir tantos “movimientos”.
Mantener inventarios lo más Lean posible dentro de la planta, reduce la necesidad de manipular material; lo mismo sucede al entregar mercancía directamente a la línea de producción en lugar de hacerlo a un almacén.